
When used together, the two are referred to as Lean Six Sigma, a process that reduces and manages different types of waste in organizations.
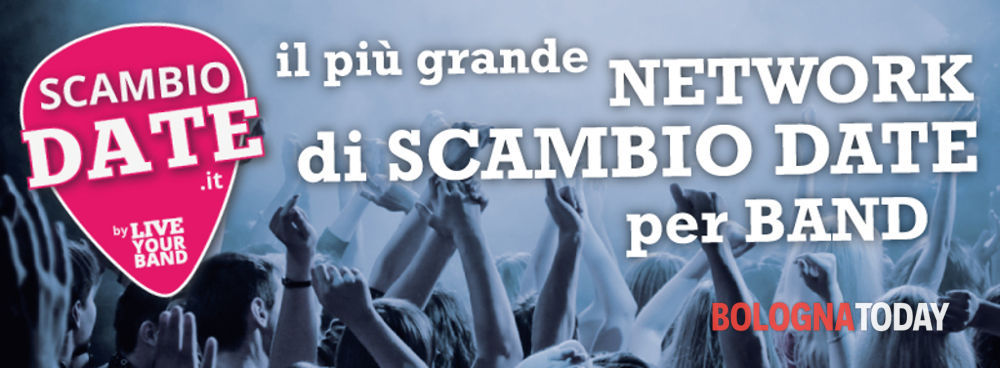
Though there are some differences between the two frameworks, the underlying philosophies behind Lean and Six Sigma complement each other exceptionally well: Lean tools are designed to eliminate invaluable processes, while Six Sigma focuses on lessening variation within a process.
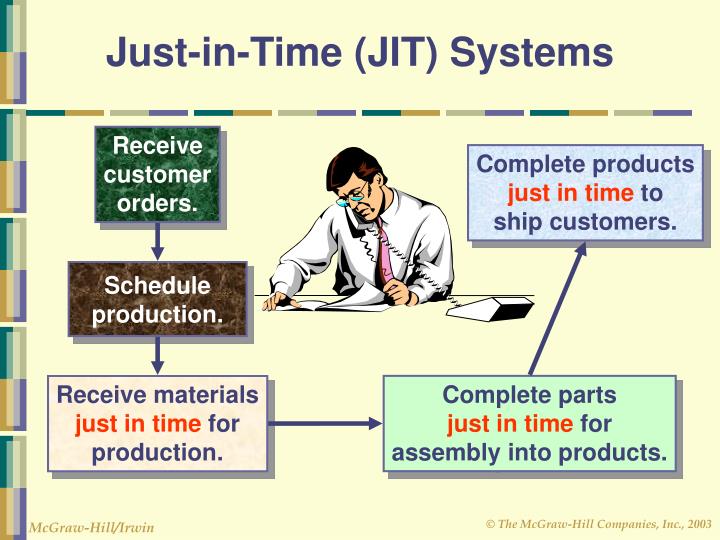
Lean tools are utilized across many industries-from manufacturing to engineering to finance- and organizations often leverage them together with Six Sigma methods. In other words, Lean tools seek to eliminate processes that aren’t valuable. The Japanese word for waste is muda, which is defined as “uselessness.” Lean tools are designed to reduce Muda in organizations and improve quality control. In this article, we’ll explore what Lean tools are and discuss the applications for seven common ones that you’ll encounter in Lean Six Sigma. In addition to being the first to correctly implement the Lean tool Just-In-Time, for example, Toyota is also known for creating its own Lean Production System. Lean methodology also has an expansive legacy outside the U.S., with companies such as Toyota making considerable breakthroughs in the application of Lean Tools throughout the 1930s. Lean tools got their start in America as early as the 1900s, when Henry Ford used Lean methodology to create the Model T assembly line. If you’ve heard some buzz about Lean tools and principles, you’re not alone.
